Plastificeringsprocessen
Det egentlige mål med plastificeringsprocessen er at overvinde de kræfter, hvormed molekylerne hænger sammen – den indre tiltrækningskraft mellem molekylerne – og derefter lejre dem i en ny form.
Hanken i en bærepose kan blive meget lang, hvis vi har fyldt lidt for mange varer i posen. Det, der egentlig sker, er, at molekylerne flytter sig i forhold til hinanden, og at de retter sig ud på grund af trækket fra varerne og varmen fra hånden. Man kan også sige, at man overvinder den indre friktion i plastmaterialet eller den indre tiltrækningskraft mellem molekylerne.
Det er disse såkaldte forskydningskræfter, vi skal overvinde i ekstruderen. Det sker ved at tvinge materialets molekyler til at glide mod hinanden under transporten gennem ekstruderen.
Når snekken roterer, vil der foregå en fremadrettet transport, idet udfræsningen i snekken ligger som et gevind med meget stor stigning. Den maksimale transporteffekt må være, når materialet bevæger sig i en ret linje, parallelt med snekken. Den minimale transporteffekt er, når materialet følger snekkens rotation.
Under tragten (traverszonen) presses materialet ind i ekstruderen som granulat eller pulver. Der er altså mellemrum mellem plastkornene, hvori der findes luft. I kompressionszonen klemmes materialet sammen, og luften fortrænges hen imod tragten. Samtidigt sker der en trykopbygning hen imod værktøjet. Trykkets størrelse er også afhængigt af modtrykket i værktøjet og af eventuel filter/si.
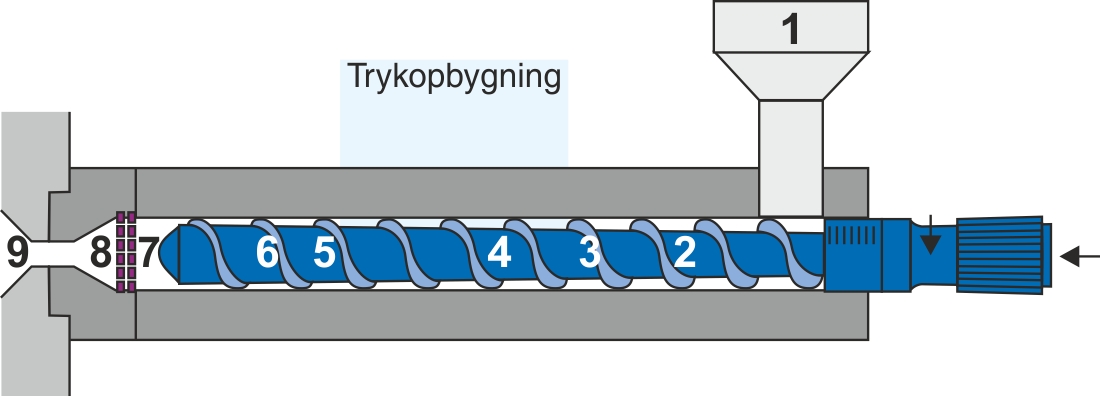
Plastificeringens procesforløb
Ved fremstilling af en homogen plastmasse under højt tryk – ud fra granulat – ved enkeltsnekkeekstrudering er der ni trin i processen.
- Råvare ind.
- Sammentrykning og opvarmning.
- Smeltning på overflade af cylinder.
- Materialet er her i paknings-elastisk form.
- Materialet er her smeltet og under maks. tryk.
- Smeltet materiale blandes her.
- Materiale filtreres gennem si.
- Materialerotation stoppes gennem hulplade.
- Materiale formes til rundt tværsnit