Køling
Efter formgivningen skal produktet køles ned. Det kan ske ved berøring mod vandkølet metal, fx valser til køling af plader eller en kalibrator til køling af rør. Ujævnheder i plader bliver rettet, ved at pladen passerer mellem et sæt vandkølede valser, som samtidigt køler overfladen på pladerne.
Røret får den glatte udvendige overflade, ved at det føres ind gennem et vandkølet stål- eller messingrør, også kaldet kalibrator. Et overtryk inden i plastrøret, eller vakuum i kalibratoren uden om plastrøret, presser/ suger plastrøret ud mod den omgivende stål- eller messingrørskalibrator. Derved køles og glattes den udvendige overflade på plastrøret. Rindende vand, brusere eller kølekar fyldt med vand fjerner ofte den sidste rest af varme fra emnerne.
Profilindustrien anvender en tilsvarende kalibrator som ved rørene. Her har kalibratoren blot den samme facon som profilet.
Luftblæsere eller køleluft anvendes i folieindustrien. Men ofte anvendes en kombination af flere kølemetoder.
At køle materialet er, modsat opvarmning, at fjerne energi, indtil det frembragte produkt er stift nok til at holde sin form. Emnet skal afkøles af det kølende medium – vand, luft eller metal, hvorved varmeenergien fjernes. Jo bedre kontakt, og jo lavere temperatur kølemediet har, desto bedre køler det.
En ting, man skal være opmærksom på vedrørende nedkøling af plast, er, at det tager lige så lang tid at nedkøle materialet, som det tager at op-varme det. Det medfører ofte, når man anvender en kraftig køling, at man får ”indefrosset” nogle spændinger i produktet.
Plastmaterialer skrumper meget. Hvis man fx køler kraftigt og længe med en vandkølet kalibrator på et rør, vil den ydre del stivne. Røret vil så få den størrelse, som kalibratoren har. Men hvis der kun køles kort tid, vil den indre del af røret få en langsom, naturlig køling og vil, samtidigt med at det bliver koldere, blive mindre. Den tynde, stivnede ydre skal er ikke i stand til at modstå trækket fra svindet i det indre rør, og diameteren bliver mindre.
Lav produktionshastighed giver større diameter. Høj produktionshastighed giver mindre diameter.
Ved høj produktionshastighed opnås kort køletid og ringe køling af røret, hvilket medfører stort eftersvind.
Ved lav produktionshastighed opnås længere køletid og god køling af røret, hvilket medfører mindre eftersvind.
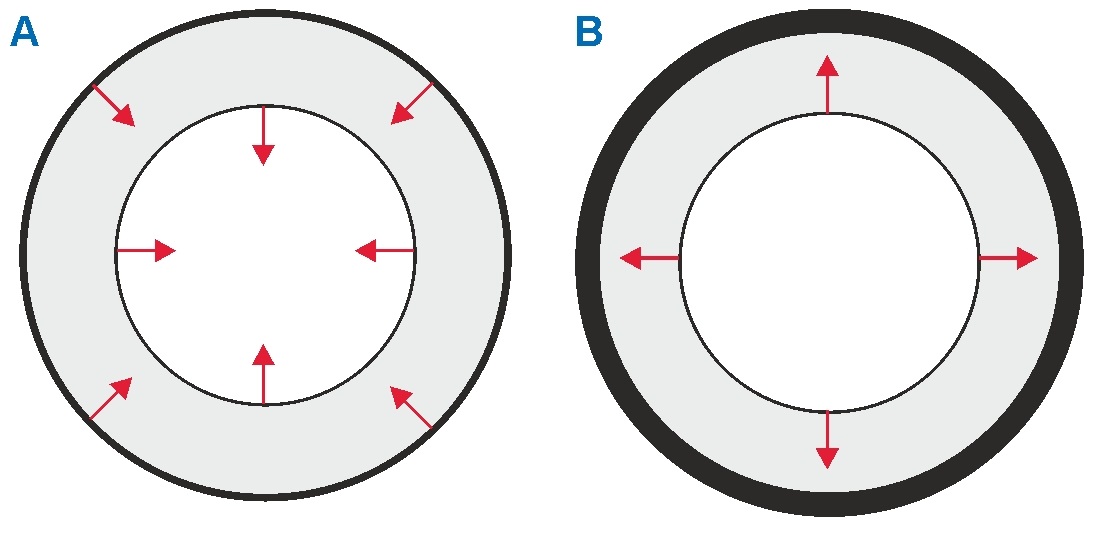